
I know, this was already finished, so why start over? I was going to attach the springs to the pulley bracket but worried they might loosen the sheet metal screws over time. I had laid up 5 bid over the area, but just wasn't comfortable with sheet metal screws even with the thickened glass substrate. I ran it by Dennis, the A&P who has been my advisor on both planes and he didn't like the idea of sheet metal screws at all. He also suggested that I should have fire sleeved the push pull cables. This meant everything I'd spent last weekend on had to be cut out and redone. More education and recreation. I'll put in aluminum hard points, sheet metal screws and star washers. No more waking up wondering if I could have done it better and safer.
_______________________________________________________________
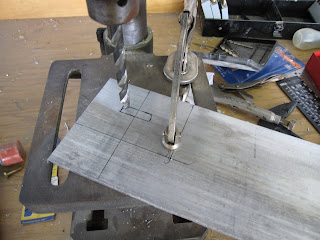
Time to make some hardpoints. I laid them out on some 1/4 inch aluminum stock and drilled the ends of the notches then off to the bandsaw.
_______________________________________________________________
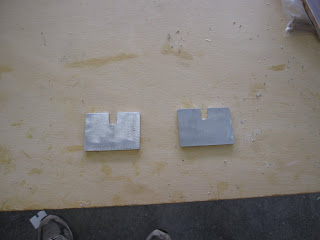
Here are the finished hardpoints ready to install. Note that they are deeply scuffed for better adhesion.
_______________________________________________________________
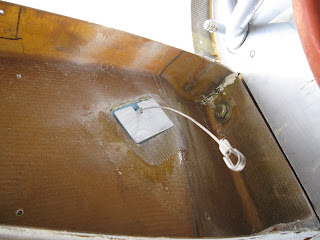
Well, the new hardpoint fits nicely and just needs to be bedded in micro and glassed over with 2 BID.
_______________________________________________________________

Here is the hard point all cured and ready for drilling and tapping. It only took 1 hour from install to fully cured. If you heat a West 405 layup with a heat gun it cures in minutes. Now I need to put the stainless piece back in place and drill and tap through the holes I made for the sheet metal screws.
_______________________________________________________________
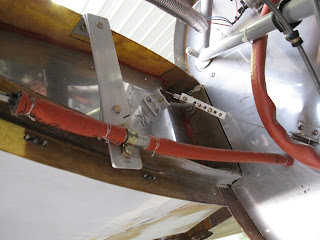
Here is the pilot's side all done. I installed fire sleeve on the aileron push pull tubes, remounted the stainless wing root fireproofing, riveted it in place and sealed it with high temp RTV. I also installed a helper spring on the rudder cable. It gives a nice positive return to neutral rudder position after deployment. It attaches to the unused hole for the cotter pin in the pulley assembly and then to a drilled bolt through the cable adjuster. It is much sturdier than with sheet metal screws and worth the extra day of disassembly and revision.
_______________________________________________________________
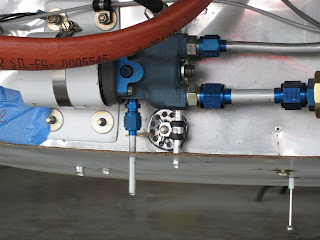
_______________________________________________________________
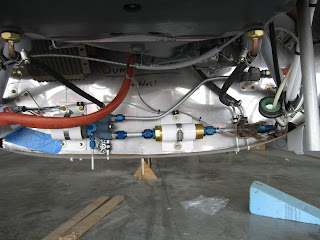
Here is a picture of the bottom with both Rotalocs visible. I have one pushed against the firewall with two clamps on a fuel line and one wedged there with a popsicle stick. Yes, I trimmed the drain from the Weldon fuel pump closer to the fuselage. I just forgot to get a picture. My back is totally done and its 8:00 - time to go home. I'll hopefully finish up the very last work in the engine compartment this week. That will truly be a builder's moment.
_______________________________________________________________
No comments:
Post a Comment