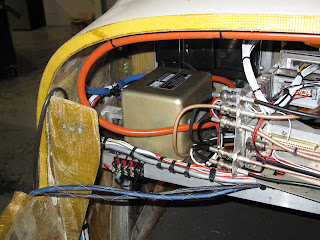
I have been spending every Saturday in the fuselage doing the finish up work. There is a lot of it, but I am making progress. Dennis, the A& P, is doing his usual tremendous work and I am doing the grunt work glassing and installing things. I've posted some of the items that have progressed since moving the plane out to the airport.
____________________________________________________________________
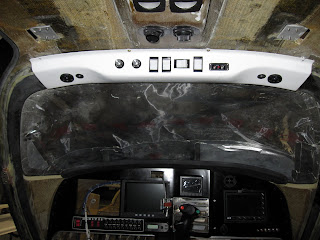
The overhead panel is wired, switches installed and mounted. I love the way it turned out.
____________________________________________________________________
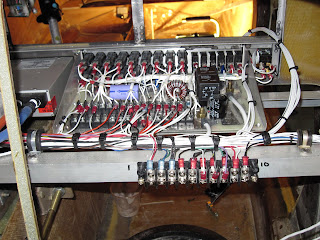
The power distribution panel is all wired up. Wow!
____________________________________________________________________
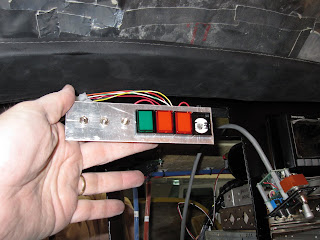
Here is the first draft of the annunciator panel that will go above the MFD's . It includes low fuel sump, Alternator fail, door ajar, boost pump running, and switches for push to test, autopilot disengage and trim disengage.
____________________________________________________________________
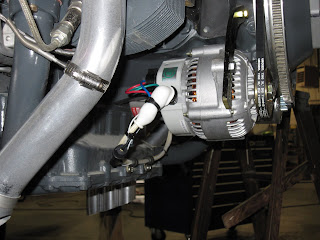
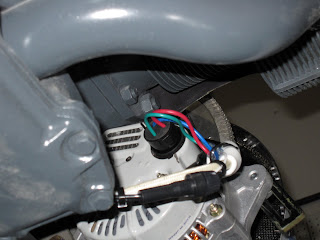
Here is the completed alternator installation. In the bottom picture you will note the stock pigtail harness installed for the wiring. Velocity simply uses spade connectors to the three terminals in the alternator. I really wanted a solid, weatherproof connection, so I bothered the NAPA guy with pictures and measurements until he found this. ( I didn't even know that it was called a "pigtail harness" - more education and recreation) I also bought and returned about 10 alternator belts before I got the right size and style. This is a big pain as installing the belt entails removing the prop. The side view shows the size code on the belt for those of you with IO540s and Nippon Denso alternators.
____________________________________________________________________
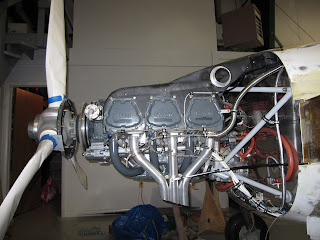
Here is a view of the copilot's side of the engine installation. You can see that most of the wiring and plumbing are completed.
____________________________________________________________________
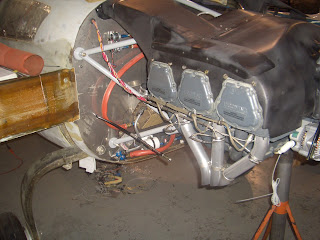
Here is a view of the pilot's side. As you will see, I needed to mount the oil cooler somewhat higher as I ran out of space lower down. This means that the flange on the side of the plenum runner would be really awkward for the SCAT tubing to the cooler. It would be much better to have the flange on the bottom of the runner.
____________________________________________________________________

This is what's so great about fiberglass. Hole in the wrong place? Cut out the part, superglue in a piece of fiberglass stock, glass and peel ply inside out. Voila, the flange is in the new place and looks as good as new as you will see in the top down view below.
____________________________________________________________________
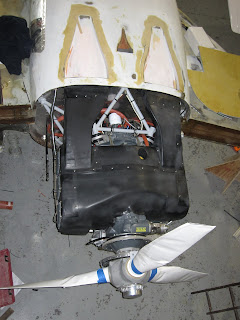
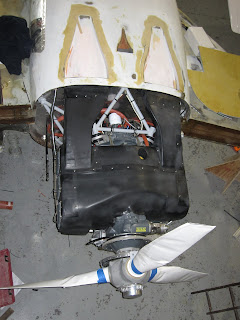
Here are some top down views of the finally installed plenum and runners. You will note that the pilot side runner looks good as new.
____________________________________________________________________
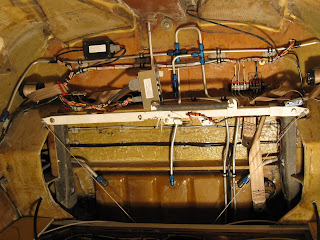
Here is a shot of what's been going on with the firewall. You will note that the plumbing and electrical are done. The gear microswitches are installed. You will see the tan seat belt inertial reels at the top corners. The box with all the wires laying on its side on top of the spar is the EIS for the GRT system. I couldn't use the mount I was so proud of. The wires stick out too far in the back. That's OK though. I've decided to mount it in the vanity panel. Might as well have access to it. The black box at the top left is the manifold pressure sensor for the GRT.
____________________________________________________________________
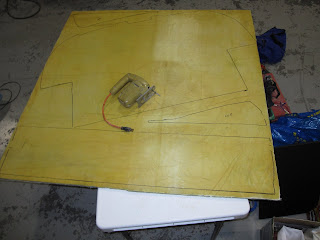
On my last Velocity I used 1/4 inch plywood for the vanity panels - heavy and flimsy. This time I laid up a 3/8 inch sheet of Divynicel foam. Much lighter and stronger, but 20 times more expensive. You will recall that I previously made up cardboard templates and fit them in place. I used them to lay out all the parts on my sheet of foam panel.
____________________________________________________________________
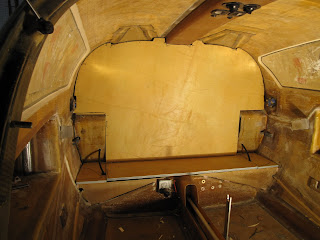
Here is the completed vanity panel set up for the back. The sides of the baggage shelf will be glassed down and the middle portion of the shelf will be removable for access to the mechanicals beneath.
____________________________________________________________________
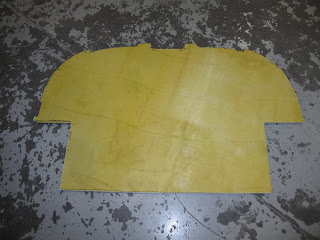
Here is the completed one piece vanity panel for the back of the baggage compartment. The next problem which presented itself was how the heck to put mounting flanges behind it, since it is one piece? I'd have to be able to reach through the middle somehow......
That's it! I'll get some MDF and make an identical panel with the middle cut out. Then I can easily reach through the middle to glass a flange all the way around the perimeter.
___________________________________________________________________
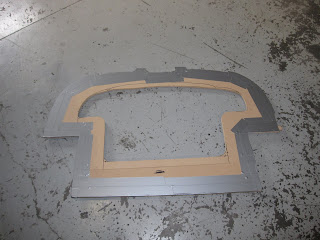
Here is the completed flange fixture ready to put in the plane. I will lay up glass from the fuselage sides, transverse bulkheads and floor of the baggage compartment cover directly onto the duct tape.
____________________________________________________________________
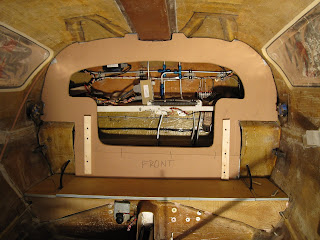
Here is the flange fixture in place with the back duct taped and ready to glass in the flanges. As you can see, this will be an easy reach on all sides. After cure, I'll pop out the fixture, trim the flange, drill some holes, add nutplates and voila!
___________________________________________________________________
No comments:
Post a Comment